This was another long and busy week.
It started on a drizzly Sunday with a barbeque and golf tournament sponsored by Beaver Mountain Log Homes for invited contractors and their guests. Other participants included the Beaver Mountain workers and owners and suppliers of BMLH. Don Adam and I attended. I don’t play golf, but Don and Adam teamed up with a pair of folks from BMLH and finished 8th out of 13 teams in the best ball tournament. The food was great and the French Woods Country Club was a beautiful place with several BMLH structures along the course and a clubhouse also manufactured by BMLH.
Then Monday rolled along and we were back to work. Jim rejoined us. The four of us made quick work of the remaining plywood roofing.
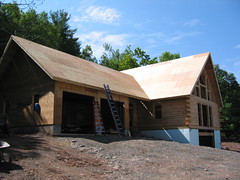
Monday was spent finishing the plywood sheathing on the roof. The place is very definitely starting to look like a home.
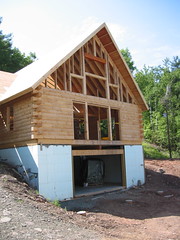
You can get a feel for the window placement in this view. The 1/2 inch sheathing still needs to be applied to the gable end.
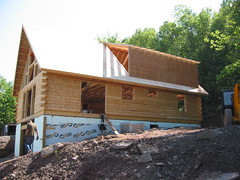
A before view of the western elevation taken on Tuesday afternoon before we began constructing the covered porch.
On Tuesday we were back to just three of us as Jim had some business to attend to. We started on the construction of the deck of the covered porch. After wrestling with a concrete pier or two to get it in the correct position, we framed out the deck’s floor joists.
Tuesday night, Don and I spent some time dismantling a bunch of pump jacks and loading them in Don’s trailer for use on the log home. We had the help of Troy, Don’s older son since the jacks were at a neighbor’s home.
When Jimmer returned on Wednesday, we laid the deck floor, erected the posts, header and rafters. We even got a start on the 2x6 tongue and groove roofing. I did most of the cutting while Jim and Adam positioned and nailed or screwed everything together.
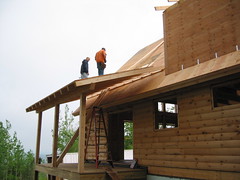
The covered porch nears completion as Jim and Adam install the last of the 2x6 tongue and groove roofing on Thursday morning.
Thursday morning Adam, Jim and I finished the wood roof on the porch and moved on to the final roof. This involves drip edge, ice and water shield, felt paper and finally shingles.
Don erected the pump jacks on the front of the garage and the east side of the house. He then put up the drip edging all along that part of the house so it is now ready for the final roof. We got chased off the job a little early due to a chilly rain that interrupted us twice in the afternoon. When we left, it was drizzling but just a few miles down the road, there was no rain at all.
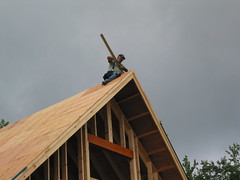
Don applies some drip edging to the peak of the gable.
Friday also promised rain and we got some early that chased us off the roof for a bit. (Plywood gets mighty slippery when wet. Not that I would know, Don, Adam and Jim were on the roof while I did cutting of shingles on a table under the roof.)
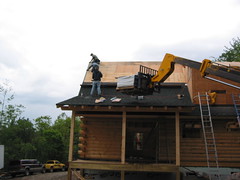
Ice-and-water, felt paper and shingles get applied to the porch roof and one quarter of the house roof.
After a half hour delay, we were able to get back to work with the sound of thunderstorms all around us. Eventually, we even had a couple of hours of sunlight. Regardless, we worked through lunch and finished about a quarter of the house’s roof before quitting around 4 in the afternoon. (Those thunderstorms were bringing torrential rains to the valley just to our west. I know because I had to drive through them on my way back to NJ.)
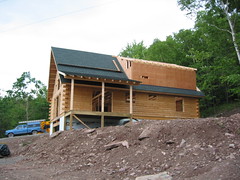
One quarter of the house is roofed.