The main portion of the walk-out basement will have 8-inch thick poured concrete walls sandwiched between 2-inch thick styrafoam sheets. The forms come with ties already installed and look like very large Legos with the tops and ends removed. These blocks get glued to one another but also lock together with “teeth”—for want of a better word. Doors and windows are cut in and capped with pressure treated 2x lumber. Holes are also cut for water pipes and electrical wires and these are filled with PVC pipe. Only three windows (2 Bilco windows for emergency exits and the one bathroom window) had to be let in. The walk out portion will be stick framed for two French doors and two windows.
Of course I took pictures.
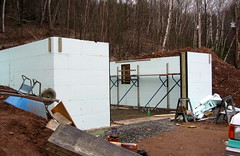
Here you can see the opening for the walk-out wall. One French door will be flanked by two large windows that go nearly all the way from the ground to the top of the door.
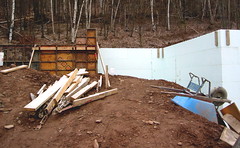
This picture shows the transition from the foam of the basement to the shorter frost wall that will be the base of the garage. The metal plates on the left are for the garage. The wall on the right is the main part of the basement and the short wall directly in front is that of the utility room which lies beneath the main entrance to the foyer and laundry room.
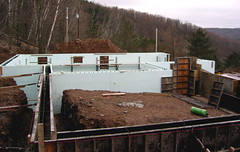
This view is from the east end of the house. You are looking over the garage to the utility room and main basement. The garage’s foundation is a 40” frost wall, most of which will be below grade.
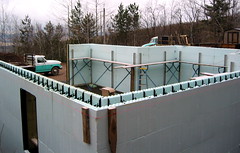
From the southwest corner you can see the bracing and scaffolding used on the inside of the wall.
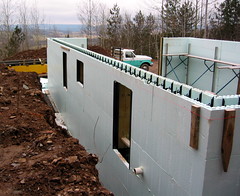
Looking along the west wall you can see the three window openings that have been cut into the forms as well as the PVC pipe that will be the channel for the electrical service.
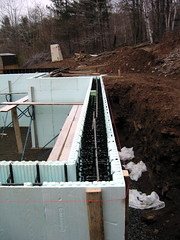
Looking into the wall you can see the mesh that serves as a tie between the two styrafoam panels and the rebar that is laid in to strengthen the entire system
1 comment:
I have read about this "sandwich" type construction but it was several years ago. Is it commonly used in your area? I understand that it's very efficient especially in colder climates. How much will be covered by surrounding soil? I have also read that it's much more economical than some other semi-underground type constuction. It appears like a possibility for tornado and high (obviously non flood plain) hurricane country but only if one has property with sufficient hillside space. Sometimes difficulty to find such property only a hundred miles north of New Orleans.
Post a Comment